THE FUTURE IS BESPOKE
Posted on April 11, 2016 in DIY
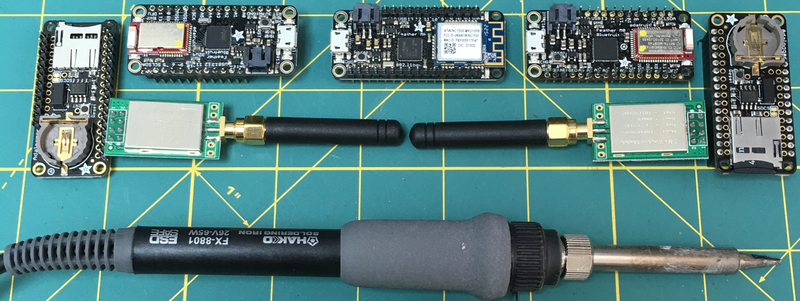
bespoke |bəˈspōk| past of bespeak. adjective [ attrib. ] chiefly British (of goods, especially clothing) made to order: a bespoke suit.• (of a trader) creating made-to-order goods: bespoke tailors.
We’re in a really interesting inflection point again in technology. Despite what you may have read, it’s not all about chat-bots being subverted by Internet trolls, or the not-good-for-anyone-really so-called “gig economy,” or even the flameout of a lot of the yummy (but overpriced) grub-on-demand startups… it’s about the reappearance of actual bespoke manufacturing and how that may well fundamentally accelerate business/product development cycles and the creation of new businesses.
TechCrunch had a really interesting piece today on micro-manufacturing – which is the idea that instead of huge manufacturing plants serving hundreds of clients – that a more efficient route for many businesses will be local, small batch facilities. TechCrunch posits the idea that the time of off-shored, mass production and of trying to manage global supply chains, remote production lines (esp. in China), etc is coming to an end and that we’re seeing an across the board local manufacturing renaissance.
They give a number of reasons for this, but the big take-aways are IP theft (again, mostly in China), management burnout and the availability of tools to do short run production that don’t require multi-million dollar plants yet that still give companies fast-turn production capabilities with agility that even Asian contract manufacturers can’t approach.
This is truly revolutionary if it can be harnessed… (spoiler alert – it can) but before we get into that, how did we get from a position where no one in their right mind would on-shore manufacturing – especially electronics – to the idea that there’s money to be made in doing it local and doing it small?
Thank Your Local Hipster
No, seriously. Hopefully you haven’t sprayed your artisanal coffee all over your laptop. Despite their haughty, fixie-riding, pumpkin-scone-eating, overly-precious attitudes and pretentiousness… hipsters really did set the stage for an artisan renaissance that is going to reach out and shake the manufacturing economy up in a fundamental way.
All snark the expense of hipsters aside, so what are we really talking about here? High-value local design and manufacturing.
In a nutshell, if you’ve ever seen Bladerunner, you probably remember the scene when Leon and Roy pay a visit to Hannibal Chew — who is a specialist in custom artificial eyes that are put into replicants. Chew makes superhuman eyes and sells them to the Tyrell Corp. Other specialists make artificial animals, from Owls to snakes. The point here isn’t Bladerunner in particular it’s the super-specialization in the high-value creation of things that need to be delivered just in time and are not amenable to large volume production. (Yeah. Bladerunner is a pretty dark example to use… but it’s on point and pretty unforgettable.)
Okaaaay…. so…how did we get here? Where is this going, exactly?
Well, back in 2006 a little Internet book seller launched a product that fundamentally changed the dynamics of service creation on the Internet and in effect launched the Web2.0 era. That company was, of course, Amazon, and the product they launched was Amazon Web Services (AWS). With AWS, what used to be a commitment of ~$100,000/year or more in instantly obsoleted hardware, co-lo fees for cramped racks and obscenely high bandwidth charges turned into a few hundred per month to launch a product serving millions. The cost of trying out an idea was reduced to a few weeks/weekends of coding time and a credit card. Best of all if your idea failed you shut it all down and tried something else: No fund-raising, no VC pitches, no ISP contracts, no hardware fire-sales and contract kill-fees at your data center. Conversely, if things went well, scaling up was as easy as adding more virtual servers – seems pretty obvious now, 10 years on, but in 2006 it was the stuff of SciFi made real.
2006 to 2010 saw thousands of new online services, but it also saw some other pivotal events: release of the Arduino, the birth of the Maker Movement (and the first MakerFaire), and the realization that if you wanted to make something cool, something unique …even, dare I used the term — something artisanal, there might well be a micro-niche you could fill. Maybe even a nascent paying market you could capitalize on. And, you could — without having to try and compete in the hotter-than-the-sun App marketplace — be all indie, and cool, and well.. a smug, aloof, cooler-than-thou Hipster. (…see! It did come back around…).
The ability of people to tap their inner self-idealized artisan has powered the post web2.0 DIY movement. It started in tech but quickly branched out to the kinds of things people have always done – from traditional crafted goods like sweaters and socks to artisanal coffees, custom bikes, art, t-shirts, … the works. And by the 2010’s there were lots of your fellow hipsters who were clamoring for the most cool, the most artisanal of whatever what the “it” thing of the moment.
Don’t believe me? Go look at Etsty – they saw an artisanal marketplace being totally ignored by eBay (in ~2006 eBay was all about selling your old junk) and made a market place for arts and crafts.
I don’t need to recount the whole history of the maker movement and all its innovations and its democratization of previously inaccessible technologies like computer-controlled milling machines (commonly called “CNCs”), vacuum formers for making molds and formed plastics, to plasma-cutters and the like. These are tools that can be found in many local TechSpaces around the country, but the availability of all these goodies lead directly to the development of crowd funded services like Kickstarter and IndieGoGo that saw a need to help all these makers to reach wider audiences by building actual businesses. Suddenly people could make cool tech in their basements, seed a market, build a brand, and completely bypass traditional funding sources and go directly to early adopters to help bootstrap their businesses.
Build Local / Ship Global
So.. what does this mean for micro-manufacturing and how is it going to shake up the economy? Maker-spaces/TechShops are a nascent form of local manufacturing systems. Some maker-spaces allow companies to contract to use their equipment for small run use, but this is a secondary “back-filling” use of such spaces in order to keep expensive rental spaces and expensive leased tools in use as much as possible. It is however incompatible with running a manufacturing business; it doesn’t scale for small manufactures since they need reliable access to be able to fulfill contracts.
However, like most things, these developments take time but the advancement in tooling is well underway. With everything from CNCs like the OtherMill and 3D printers (MakerBot, LulzBot and a host of others) to the creation of small-scale Pick and Place machines like the FirePick Delta we are fast approaching a point where small-scale manufacturing will be cheap to create and very highly profitable to operate.
These people are the “arms-merchants” to this new economy. They are priming the pump for the very companies that TechCrunch references as trying to find something better: a new way to realize their products without worrying about having their IP stolen before their products even get to market, without having to have an outpost in Shenzhen, or becoming best friends with every TSA and border guard across 15 timezones. However, the logistics infrastructure that enabled the globalization of large form manufacturing is also the friend of the vanguard of the new micro-manufacturing movement.
For a great example of the kind of companies this movement is creating, look at AdaFruit. They make use of this global logistics capabilities to get millions of parts to people around the world to the tune of a reported $40MM per year. They’re another arms merchant – but to DIY Makers and designers. AdaFruit sells amazing little modules that implement everything from simple connector assemblies to whole micro controllers that can be used to prototype new devices (look at the article previous to this one – I use many of their controller modules in my IoT projects) or even as the building blocks of complete systems used in shipping projects. And they do this in NYC where electronics manufacturing hasn’t exactly been a staple of the economy since the death of Radio Row in the 1960s.
So how do we get there? Like most things, it’s going to take a few bold experimenters to start with what they can get – often a combination of last-gen, used, after market equipment – along with some of the current leading edge of available small maker gear like the OtherMill .. and probably some home-grown ingenuity to fill in whatever gaps remain. It will be cool to watch this develop – the barriers to entry to small, local profitable manufacturing are falling. Tomorrow it’ll be fast-turn circuit boards …. next up, those designer eyeballs.